Three tips for implementing the MDR
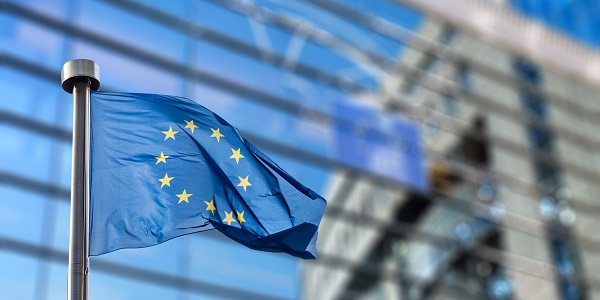
Medical device and in vitro diagnostics manufacturers, along with European notified bodies, are all navigating the unprecedented, tumultuous waters of the MDR and IVDR, with the over-arching goal being patient safety. BSI’s Bill Enos (Americas Senior Commercial Director, Medical Devices) and John Bis (VP of Medical Device Solutions Sales) offer three key pieces of advice for medical device companies trying to compete in the new EU MDR environment.
Thoroughly review and understand the full content of the MDR
The requirements for applications under the new regulation require a higher level of documentation than the old set of directives. The BSI team spends a significant amount of time working with its clients, both existing as well as prospective, to set the right expectations about what the new requirements bring, says Enos.
“Manufacturers can benefit themselves most by taking the time to truly understand what the requirements look like. That will give them a better basis for conversations with their notified bodies, with their own regulatory teams, marketing teams, and quality teams. The better and more well-versed they can be internally with the new, higher level of documentation requirements will certainly help them be effective externally.”
Submitting first isn’t necessarily best
Take the time to thoroughly review your technical documentation before you submit to a notified body. The last thing that a manufacturer should want to do is try to race to get that submission in, only to have it come back with questions or potentially having an incomplete file which gets rejected. What manufacturers can avoid is a lot of wasted time and budget in thoroughly preparing ahead of time to ensure that their files are complete before they send them. This preparation will also serve manufacturers well going forward, because then they can apply those lessons learned to all of their subsequent files,” says Enos
Invest in yourselves
In many cases, where there are gaps or weaknesses, there are opportunities out there for manufacturers to look at things like training. “The key to success here is in educating themselves as well as educating those all the way up through their organization, including management,” explains Bis. “This can often require that companies invest more in themselves: more regulatory experience, more clinical data, more quality management,” he says.
“Having well trained, knowledgeable internal teams will go a long way because notified bodies aren’t allowed to consult,” adds Enos. “We really only have the opportunity to provide a list of gaps, not necessarily solutions. So the better trained and the more well-informed the manufacturing staff is then that makes the entire review process more streamlined. When it’s streamlined, I think at the end of the day, hopefully it costs less, it takes less time and products are to the market and to patients more efficiently.”
This article is an excerpt from "BSI: Three Tips from the Top European Notified Body" which was published in Market Pathways, Vol. 2, No. 1, January 01, 2020
Request more information today for a call back from a member of our sales team so that you can get a better understanding of how Compliance Navigator can meet your needs.
The Compliance Navigator blog is issued for information only. It does not constitute an official or agreed position of BSI Standards Ltd or of the BSI Notified Body. The views expressed are entirely those of the authors.