Clinical investigations and the MDR
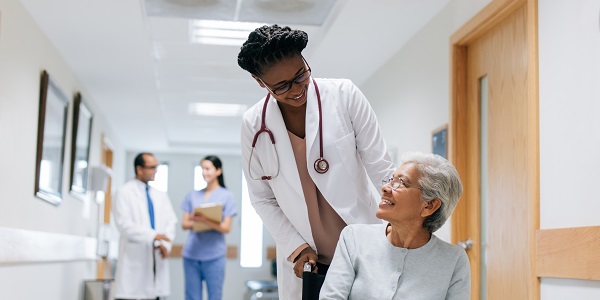
Clinical investigations are time consuming and resource intensive
Under the European Medical Device Regulation (2017/745) (MDR), there are important new requirements for pre-market and post-market clinical investigations. The conduct of a clinical investigation – also referred to as a clinical study in this blog post – is one of the most time consuming and resource intensive activities that a medical device manufacturer can face. For these reasons, manufacturers should ensure that the purpose of the clinical investigation is clear; all applicable regulations, common specifications (e.g. concerning device-specific requirements relevant for clinical investigations), international standards, European guidance documents and national guidance documents have been identified; all persons involved with the study understand their roles and responsibilities; and the study is well organized and conducted in accordance with relevant QMS practices.
The clinical investigations discussed in this blog post are generally conducted to meet regulatory requirements related to the generation of clinical data in support of safety and/or clinical performance for CE marking or maintaining the CE mark of the subject device. More than one clinical investigation may be needed. For this reason, manufacturers should clearly define the regulatory purpose for generating such data and identify the clinical development stage during which the clinical study is to be conducted.
MDR Article 10(9) requires manufacturers of devices, other than investigational devices, to establish a QMS that ensures compliance with the MDR and that addresses among other aspects, product realization, including planning, design, development, production and service provision. Clinical investigations are, in most cases, part of the design process and, where PMCF investigations are conducted, intended to demonstrate ongoing device safety and clinical performance requirements. Thus, clinical investigations are activities that should be managed under the QMS in that they are generally intended to meet the requirements of the MDR.
The development of key standard operating procedures (SOPs) for managing the clinical investigation process, within the QMS, serves the same purpose as SOPs developed for other aspects of a manufacturer’s processes. They provide clarity, consistency, and a means for avoiding errors and omissions. They will also facilitate the management of clinical investigations conducted under the Medical Devices Directive (93/42/EEC) (MDD) or Active Implantable Medical Device Directive (90/385/EEC) (AIMDD), but continuing under the Medical Device Regulation (2017/745) (MDR), or those that will be conducted solely under the MDR.
SOPs for managing the clinical investigation process are applicable not only to manufacturers deciding to manage clinical investigations internally with company personnel, but also to those that need to outsource one or more clinical investigation activity to an external vendor. In the latter case, fewer internal SOPs may be needed if the SOPs of the external vendor are used.
The availability of persons who understand the medical device clinical investigation process, whether by training, experience or both, is critical for its successful implementation. In contrast, assigning persons with little or no experience or knowledge of clinical investigation requirements and management is associated with ineffective study management, which can lead to project delays, and possibly, failure to achieve intended clinical data objectives.
This is an excerpt from the BSI medical devices white paper: Medical device clinical investigations – What’s new under the MDR? To browse our collection of medical device white papers, please visit the Insight page on the Compliance Navigator website.
Request more information today for a call back from a member of our sales team so that you can get a better understanding of how Compliance Navigator can meet your needs.
The Compliance Navigator blog is issued for information only. It does not constitute an official or agreed position of BSI Standards Ltd or of the BSI Notified Body. The views expressed are entirely those of the authors.